Behind the Scenes: The Role, Technology, and Manufacturing of Metal Oxide Varistors (MOVs) in Modern Power Systems
- Florent Giraudet
- Nov 18, 2024
- 7 min read
Introduction: The Hidden Guardians of the Grid
While surge arresters are the foundation of insulation coordination in power systems and critical components of the power grid, they are often underappreciated due to their standardized integration, relatively lower complexity compared to other major equipment, and lower costs. Despite this, modern power systems couldn't operate reliably without high-quality metal oxide (MO) surge arresters. These silent protectors play a vital role in sustaining both current and future power demands, especially as grids evolve with renewable energy sources and interconnected networks.
At the core of today’s surge arresters lies the Metal Oxide Varistor (MOV), which has become the backbone of the electrical industry’s surge protection devices. MOV technology, which became prevalent in the 1980s, is now dominant. Its historical development reflects evolving challenges and innovations, with ongoing R&D efforts focused on improving performance, reliability, and long-term stability, while also adapting to new applications.
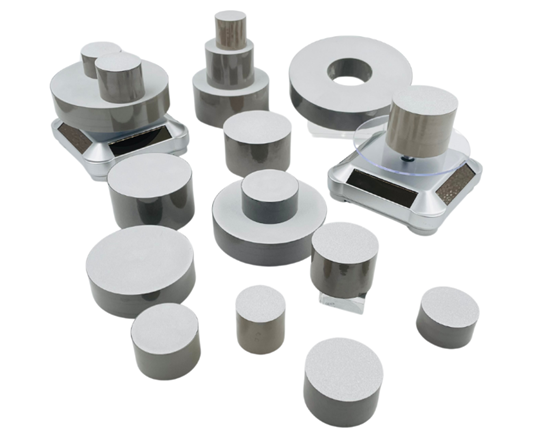
Various types and sizes of Metal Oxide Varistors (MOVs)
Why Surge Arresters Matter in a Changing Energy Landscape
Surge arresters help ensure an uninterrupted supply of electricity, even in the presence of overvoltages caused by lightning or switching surges.
The evolution of electrical networks reflects major trends that MOV technologies are adapting to address, sometimes going beyond their original functions. For instance, HVDC networks require compatibility with direct current and high energy absorption capabilities. The shift towards HVDC transmission for long-distance power transfer and complex applications, like interconnecting asynchronous networks and offshore wind farms, has led to the need for advanced HVDC circuit breakers. Here, specialized MOV applications play a major role in HVDC circuit breaker development, where these systems need to isolate faulted segments quickly without a natural current zero. This prevents large-scale outages and supports the reliable operation of multi-gigawatt DC networks.
Similarly, the interconnection of networks requires reconsideration of line architecture, prompting the construction of new high-voltage lines or upgrades to existing ones to transport energy more reliably. The integration of renewable sources, often located far from urban centers, requires highly sensitive and reliable new transmission structures. These developments demand innovations from surge arrester and MOV manufacturers, tailoring their solutions to meet these demands.In recent years, line surge arresters, particularly Externally Gapped Line Arresters (EGLAs), have garnered renewed interest. Previously overlooked, EGLAs are now seeing a resurgence, leading to a reevaluation of MOVs' roles. Unlike traditional MOV applications, which constantly experience voltage across their terminals, these newer applications require greater charge transfer capabilities to handle lightning discharges.
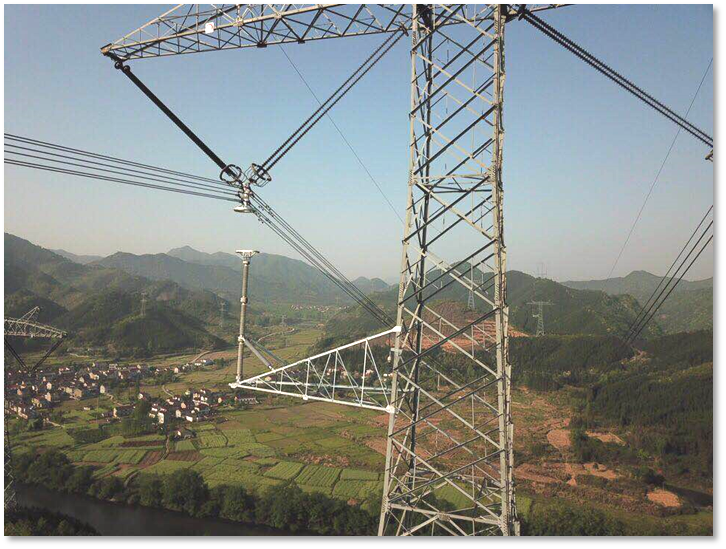
HVDC EGLA, Xi’an XD Arrester Co., Ltd., China
MOV Technology: Engineering the Perfect Protector
The core of every modern surge arrester is simply a stack of MOVs. These MOVs are strategically stacked to form one or multiple columns, each designed according to specific requirements for protection levels (residual voltage), energy absorption capabilities, charge transfer ratings, and voltage ratings to handle temporary overvoltages.
While the number of MOVs in a single column typically correlates with voltage ratings, a full MOV stack can comprise multiple columns in parallel to achieve specific energy or charge ratings. Supporting current flow depends on having the right number of parallel paths within the MOV(s). Ratings for energy, charge, or protection levels are controlled by selecting an appropriate MOV diameter or the total number of parallel columns. For construction reasons, the diameter is generally limited to around 120 mm per MOV column. Multiple MOV columns may be housed within one or more surge arrester housings, depending on the application. In summary, the MOV diameter directly influences its ability to handle high current densities from transient surges without sustaining damage.
Voltage ratings are essential for ensuring the long-term stability of the MOV stack under continuous operating voltage or specific temporary overvoltage conditions. Although MOVs are not always under continuous voltage, this remains the case for most applications today.The breakdown voltage of a boundary layer between two ZnO grains is approximately 3V, depending on the structure. To reach the desired breakdown voltage for a specific application, an MOV must contain an appropriate number of serial grain boundaries. However, due to production and testing limitations, MOV height is generally restricted to about 45 mm across manufacturers. Therefore, in high-voltage surge arresters, multiple MOV blocks are stacked vertically to meet the necessary performance requirements.

The Manufacturing Process: Where Science Meets Art
There are generally seven key steps involved in producing the final product:
i. Weighing and Mixing:
The primary constituent of MOVs is zinc oxide (ZnO), making up roughly 90% of the total mass. The remaining 10% comprises oxide additives, which serve multiple functions: they fine-tune the non-linear V-I characteristics, control grain growth, maintain the electrical stability of the MOVs, and facilitate the manufacturing process. In this first step, the zinc oxide material is mixed with the additives, which are prepared upfront depending on the product specifications and requirements to achieve different functions. For example, a typical MOV for an AC distribution system will not have the same constituents as an MOV for HVDC Circuit Breakers. A slurry is then obtained by incorporating organic solvents and binders.
ii. Dehumidification or Spray Drying:
Next, the dehumidification process, also known as spray drying, prepares the material by removing moisture. The slurry obtained during mixing is injected into the spray dryers, aiming to remove the liquid content and yield a final powder. The production of oxidized granulation powder directly affects the electrical properties of the MOVs. Key factors such as the particle size of the granulation powder, the internal temperature of the granulation tower, and the uniformity of various component concentrations significantly impact the MOVs’ performance.
iii. Pressing or Forming:
In this visually significant step, the dehumidified powder is pressed into the preliminary shape of the block. This dry pressing process is where the MOV begins to take form. At this stage, each block must be meticulously weighed and controlled to ensure precision and quality.
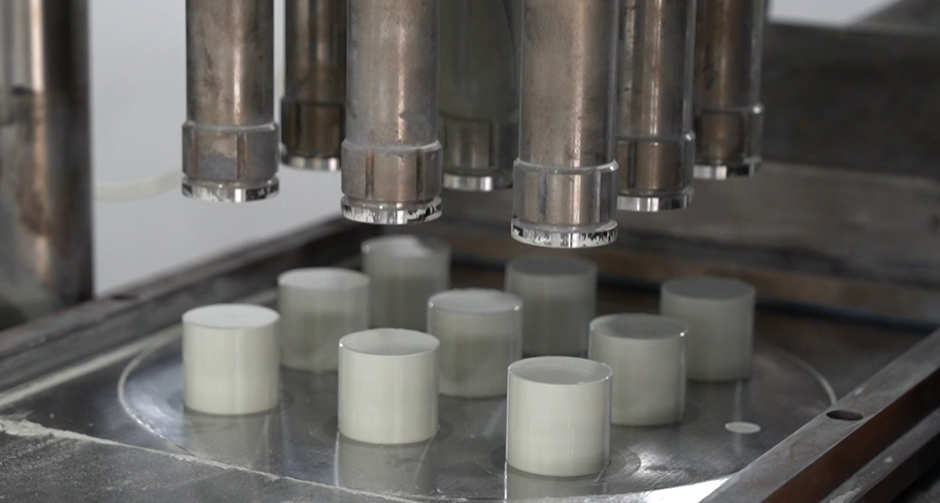
High Pressure Forming process of MOV
iv. Pyrolyzing and Sintering:
Once the MOV has its initial shape, it undergoes pyrolyzing and sintering in high-temperature tunnel furnaces. The pyrolyzing process removes organic solvents and binders from the block, resulting in a "green block," which appears green due to the natural color of MOVs. In the subsequent sintering process, temperatures reach up to 1050°C, causing the blocks to turn black externally, though the inner part remains green. This sintering step forms the grains and grain boundaries, meeting the desired electrical performance requirements. These processes remove certain compounds, causing the MOV to lose approximately 17% of its initial volume.
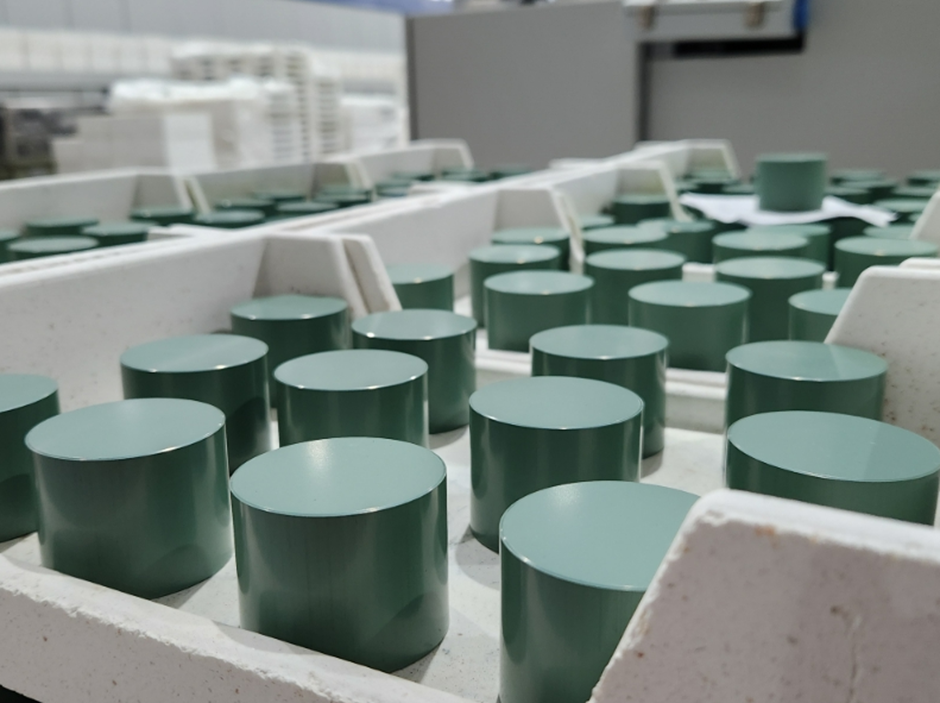
Green blocks after the pyrolyzing process
v. Passivation or Coating:
A specialized passivation layer is applied to the lateral surface of the MOV in this step. This layer is crucial for protecting the MOV from environmental factors and enhancing its flashover resistance. It's a highly sensitive process requiring expertise to produce high-quality MOVs. While different materials and processes can be used for coating, glass coating represents the cutting edge of MOV technology.
vi. Surface Preparation and Electrode Application:
After coating, the front surfaces must be smoothed to facilitate electrode application. These surfaces may not be entirely flat, and residual coating material can remain. A grinding machine combined with water achieves a completely flat surface, essential for the stacking process. Once a clean and flat surface is obtained, metal electrodes, often made of aluminum, are applied. The aluminum layer, typically about 0.1 mm thick, ensures proper conductivity between MOV blocks, allowing the energy or current impulse to be evenly distributed across the MOV surfaces.
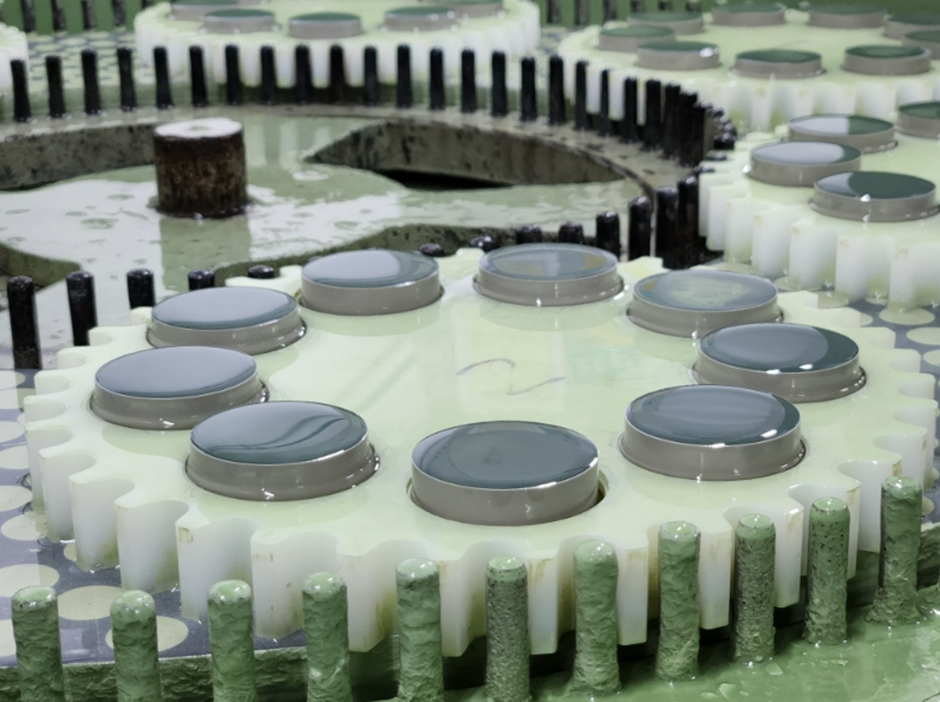
MOV surface preparation
vii. Final Verification and Testing:
Electrical tests are conducted to verify that the MOV meets specified characteristics for electrical performance and charge transfer capabilities. Like complete surge arresters, individual MOVs undergo typical electrical tests, such as reference voltage and residual voltage tests. For MOV manufacturers, an additional routine test — the long-duration current impulses test — is critical to ensure the proper characteristics of the blocks, including the properties of the grains and boundaries. The rejection rate is closely tracked at this stage.
Quality Control
Quality Assurance & Quality Control are critical components throughout the manufacturing process of MOVs, with several key steps designed to ensure consistent performance and reliability.
A primary focus is on the incoming raw materials inspection, especially the zinc oxide and various additives. Rigorous testing is applied here to verify that all sub-suppliers meet stringent quality expectations, safeguarding the foundational integrity of the MOVs from the very start.
Another critical control point is the final powder inspection, conducted right before the pressing and forming of the MOV blocks. Each batch intended for pressing undergoes meticulous testing to confirm that the correct production processes were followed and that the oxidized granulation powder exhibits the necessary electrical properties. This is essential to maintain the MOV's intended performance and prevent any compromise in reliability.
Beyond these initial controls, in-process testing plays a vital role in validating product consistency. Select samples from each batch are subjected to specialized tests, such as high-current impulse and long-duration current impulse tests, ensuring resilience under various operational stresses. Additionally, an accelerated aging test, often referred to as the long-term stability test, is conducted to simulate extended performance and verify that the MOV blocks can retain their properties over time.
These comprehensive quality assurance measures collectively uphold the MOV's reliability, ensuring that each unit is equipped for demanding applications in power systems.
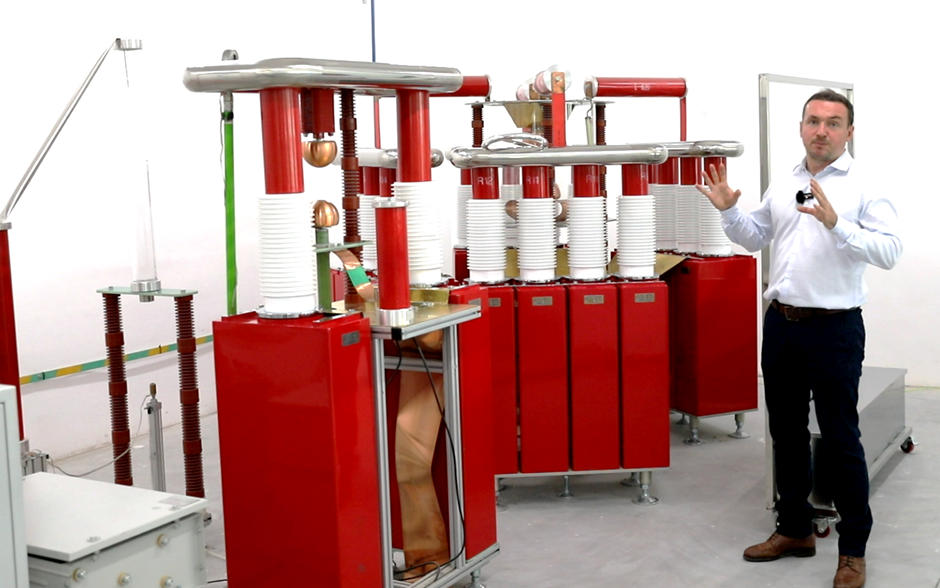
High Current Impulse Generator achieving 200kA at TGE R&D center
Conclusion: A Look at the Unsung Heroes of the Power Grid
Surge arresters and Metal Oxide Varistors (MOVs) are essential, foundational components that quietly sustain the reliability and resilience of modern power systems. As grids evolve to meet the demands of renewable energy, interconnected networks, and advanced technologies like HVDC transmission, MOVs adapt to these challenges, showcasing their versatility and importance.
Understanding the journey of MOVs—from the meticulous mixing of raw materials to the precise final testing—highlights the expertise and commitment embedded in each protective component. These processes ensure that MOVs can withstand extreme conditions and perform their crucial function, safeguarding power systems against disruptive surges. MOV technology remains a quiet guardian, but one without which the stability of the electrical grid, and by extension, the reliability of daily life, would be compromised. With every new advancement, MOVs continue to fortify our energy infrastructure, making them unsung yet indispensable heroes of the modern power landscape.
תגובות